Fingerboard & fretwork
Together, the fingerboard and fretwork are one of the most important features of a bass, so they need to be perfect. There are numerous features you do not immediately see that enhance the stability, stiffness and playability of the neck. The first step is one of the most important, and this is to start with tension-free, seasoned wood (as described under “How we build our necks“).
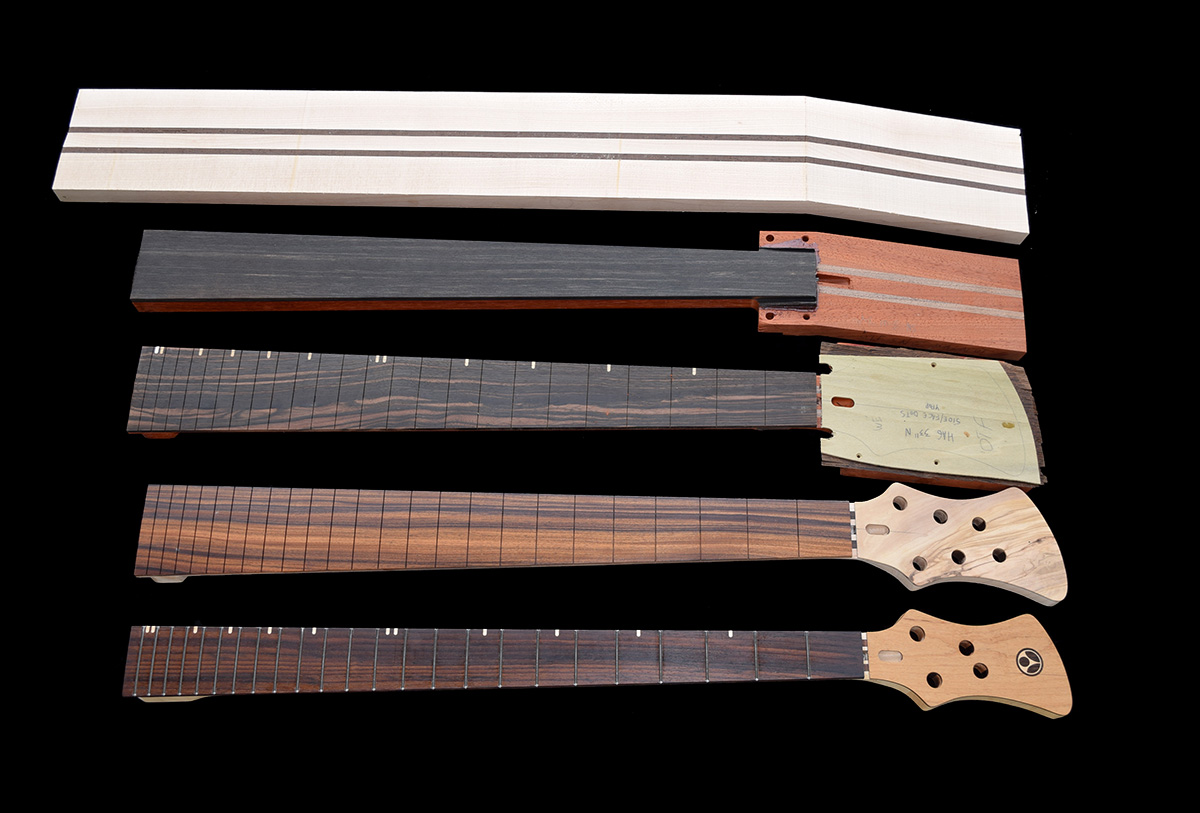
The production of the neck
In most factories, the fingerboard is radiused and the fret-slots are cut at a very early stage of the neck construction process – sometimes even before the fingerboard is glued to the neck. This is because it is quicker and much easier in terms of production.
Any wood – therefore also the neck – can move, twist or warp due to the tension that is released when the wood is cut from a piece. Each of the steps in the production process – from starting with a neck blank through to finishing with a fully shaped neck – involves extensive wood removal. This is the principal reason why we cut the fret slots and radius the fingerboard at the very end of the neck construction process.
The neck is built over several months so that the wood can expand and contract between each step of wood removal. Although we do start with our stable neck blanks, we employ this time-consuming process to minimize any chance of movement after the fingerboard has been radiused and levelled. This ensures that the flat surface remains flat once we have levelled the frets on the fingerboard.
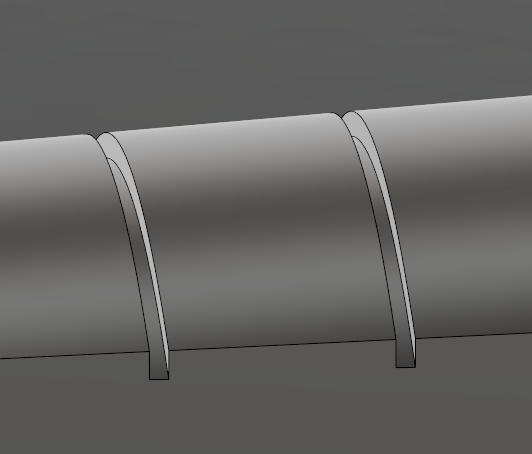
Radius and fret slots
To remove the minimum of wood and maximize the stiffness of our necks, we cut our fret slots with the same radius as the fingerboard, leaving almost no space underneath the fret. This not only makes the neck stiffer; it reduces the chance of moisture getting under the fret, which could potentially cause the wood to swell and raise the frets slightly.
We also fill any space under the frets with a special sealer that ensures the frets are attached and protected against the elements and sweat.
Our fingerboards have a compound radius. On a five-string, the radius is 26” at the nut and 30” at the 24th fret. This is slightly flatter than the industry standard and facilitates easier playing. With a flatter fingerboard, your left hand does not need to reach so far for the lowest string. This is even more important on a six-string bass.
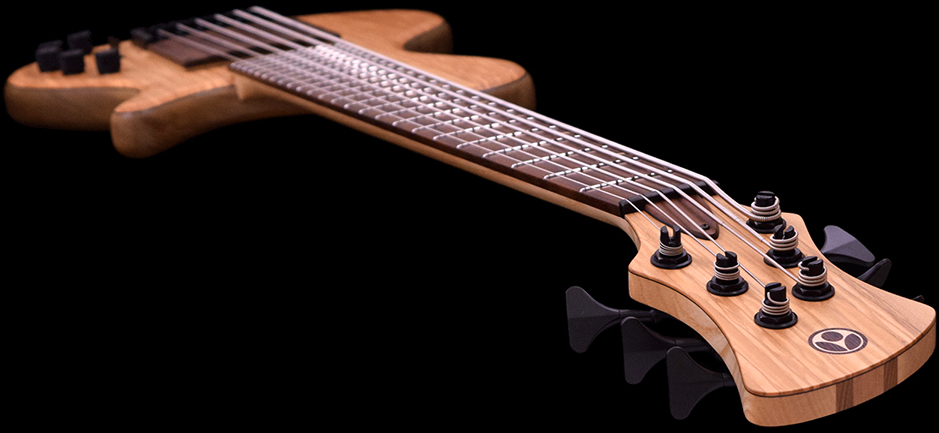
You want it level
In most cases, the frets on an instrument are levelled when the neck is not in tension, i.e. not strung. When you put the strings on, the strings start pulling on the neck and the truss rod needs to be adjusted. All these forces on the neck can result in the neck not being perfectly level, even though it was perfectly level before the strings were put on.
We level our fingerboards with the neck under the same tension and forces it would be under when strung and tuned up. This proprietary method is complicated and time-consuming, but enables us to ensure that the fingerboard and frets are perfectly flat when the instrument is strung.
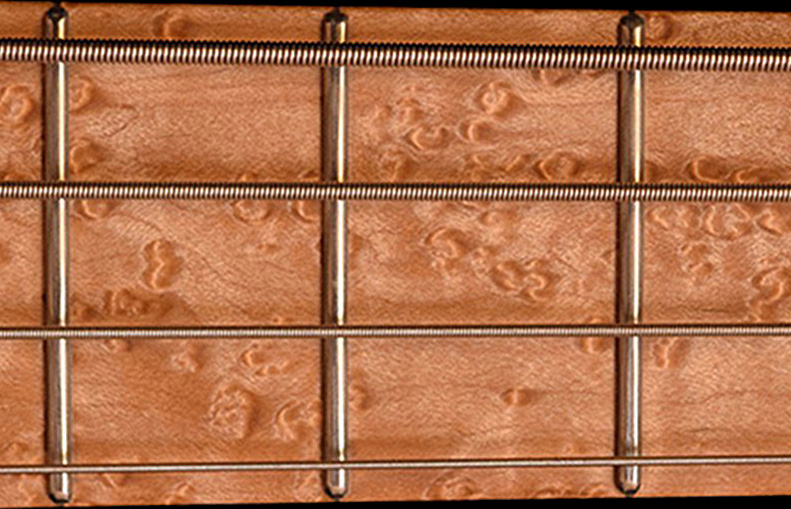
Smooth edges
For an extra-smooth feel, the fingerboard edges are rounded over and the frets undergo a special treatment: The fret ends are not just filed at an angle, but completely rounded over for a sleek, worn-in feel. Each fret end is rounded off individually, by hand, and polished to give you the feeling of a decades-old fingerboard. This very time-consuming work, and something you will not find on many other basses.
This, in combination with our oil finish, makes our necks feel very smooth under your fretting hand.