How we build our necks
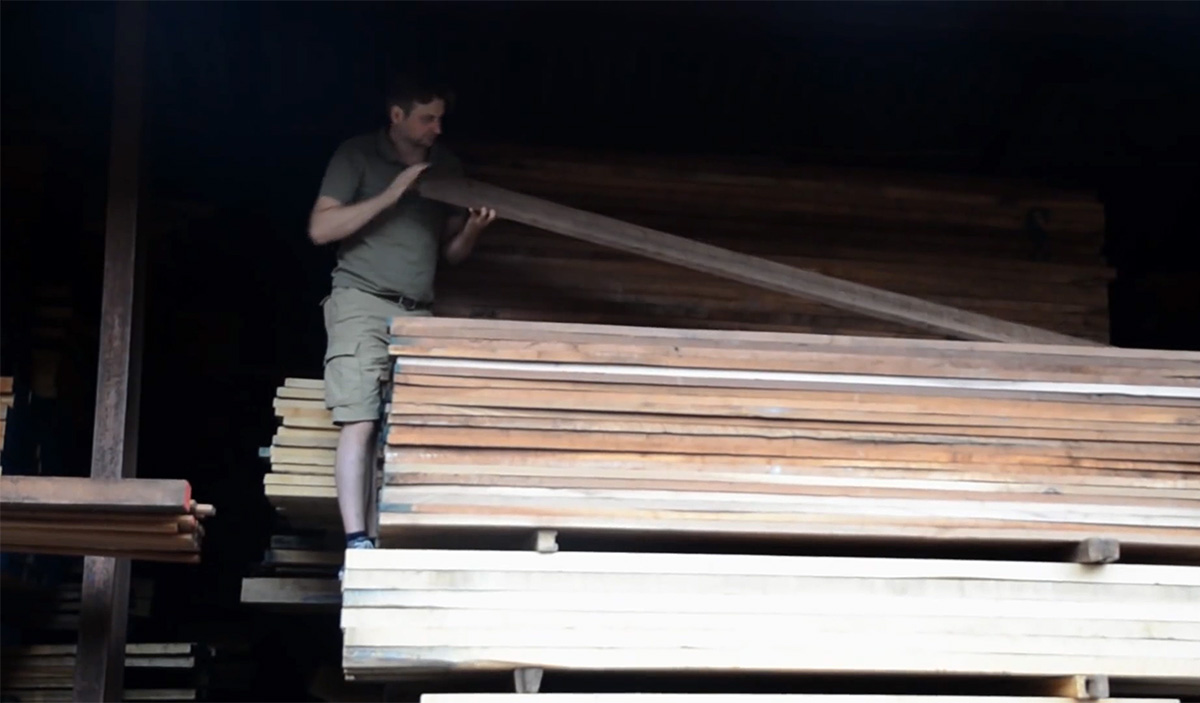
Our approach to building basses is somewhat different from that of other luthiers. For example, our neck blanks are processed and built far in advance of being used. If you were to order one of our basses today, it would be fitted with a neck we started to build two years previously!
For our necks, we purchase ready-seasoned, dry wood. We hand-pick the very straightest pieces, with fault-free, straight grain. Usually, only 5 to 10% of the wood will meet our requirements. This wood is added to our stock until it is selected for the production of our necks. It may season for many years
We start the neck production process buy selecting the right pieces from our stock, clean them up and make them ready for the neck production. we allow them to season for approximately six months and monitor how they react to changes in humidity.
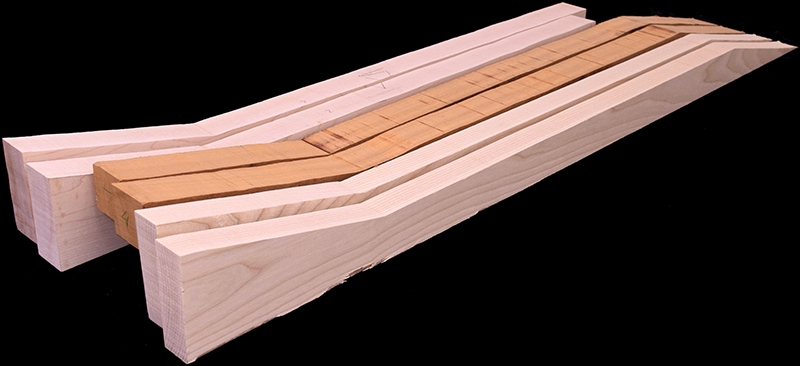
After the six-month seasoning period, we cut the wood that has remained stable into neck-sized pieces. During the cutting process, we can immediately identify any wood containing tension. Some straight pieces with perfectly straight grain can warp or twist considerably, whereas others remain perfectly straight. The wood containing tension is discarded and only the tension-free wood is kept for necks. We then allow the neck-sized pieces to season for another six months and, again, monitor how they react to changes in humidity.
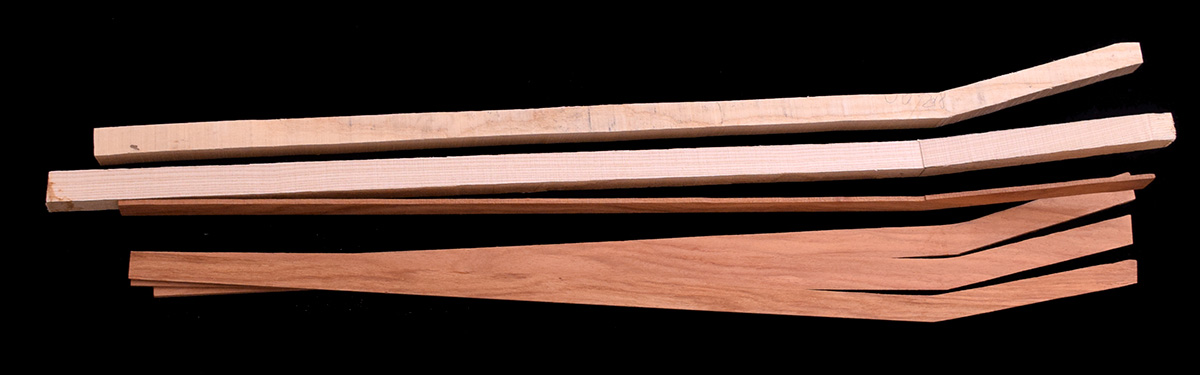
When the second wood-seasoning period comes to an end, we are approximately twelve months into the production process. At this stage, we cut the wood into thin laminates, which are very close to their final thickness. If any of the wood contains tension, this is again immediately evident, and we separate the perfectly straight pieces from the warped pieces. We then allow each thin laminate – which are now as close to their final shape as possible – to season for another six months. Again, we deliberately do not kept keep them in a humidity-controlled environment, and instead allow them to be influenced by the natural changes in weather conditions.
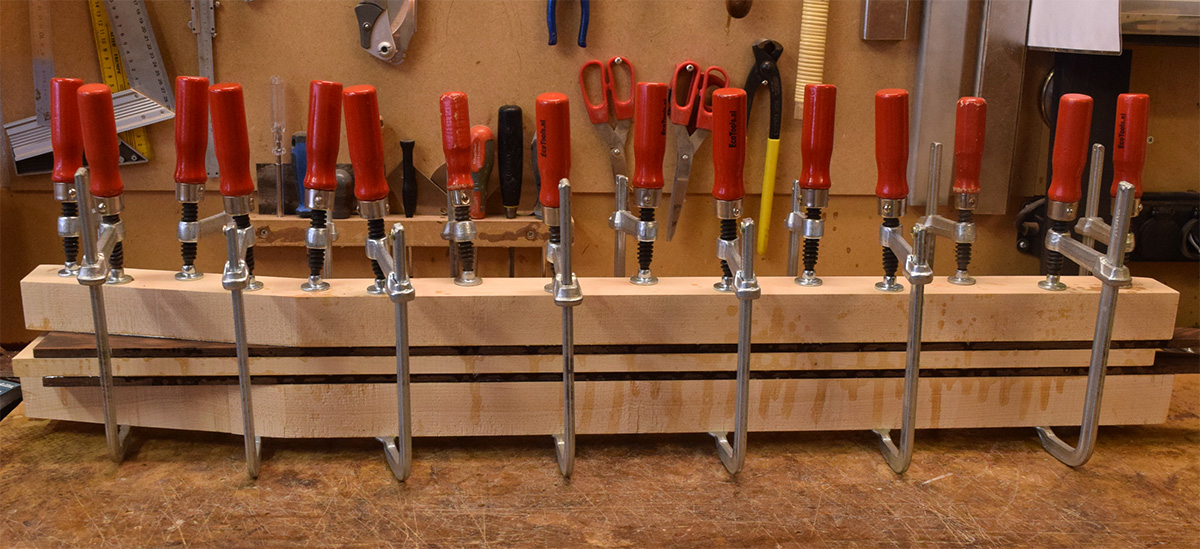
During the next stage, we inspect each individual laminate to see whether they have warped or twisted over the past six months. At this point, we are approximately eighteen months into the production process. Again, any laminates that have not remained perfectly straight are discarded, while the straight pieces are glued up to make neck blanks.
When we glue up our neck blanks, we do not use water-based glue, as moisture might otherwise get into the laminates. After gluing, we allow the neck blanks to settle for six months so we can be absolutely certain that they are stable.
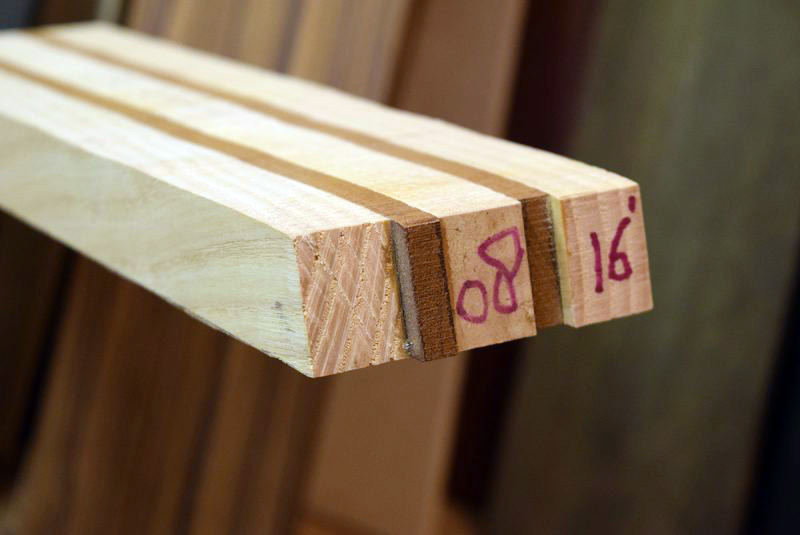
The final stage involves a further selection process, in which each neck blank is inspected. By this stage, we are approximately two years into the construction process. Only perfectly straight neck blanks are selected for further processing. At this point, we can be certain that the wood in the neck blanks is stress- and tension-free and will not cause you any problems in the future. We always have a stock of seasoned neck blanks our customers can choose from.
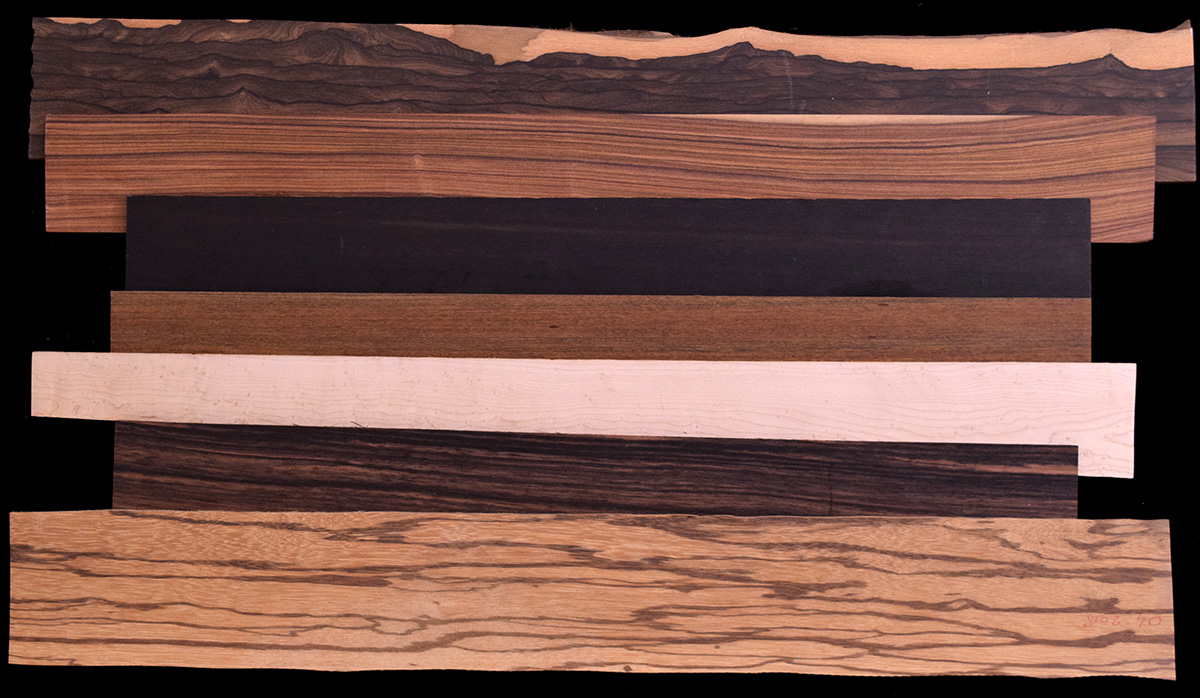
Our fingerboards are processed in a very similar way to our neck blanks, whereby they also go through a two-year selection process.
The advantage of having stable, ready-to-go neck blanks and fingerboard blanks in stock is that it allows us to start building your bass straight away as opposed to having to build a neck blank first.
Our unique neck and fingerboard production processes are time-consuming, but they ensure that your bass will have tension-free neck that will not cause you problems if you travel around the world and subject it to changing temperatures and humidity.
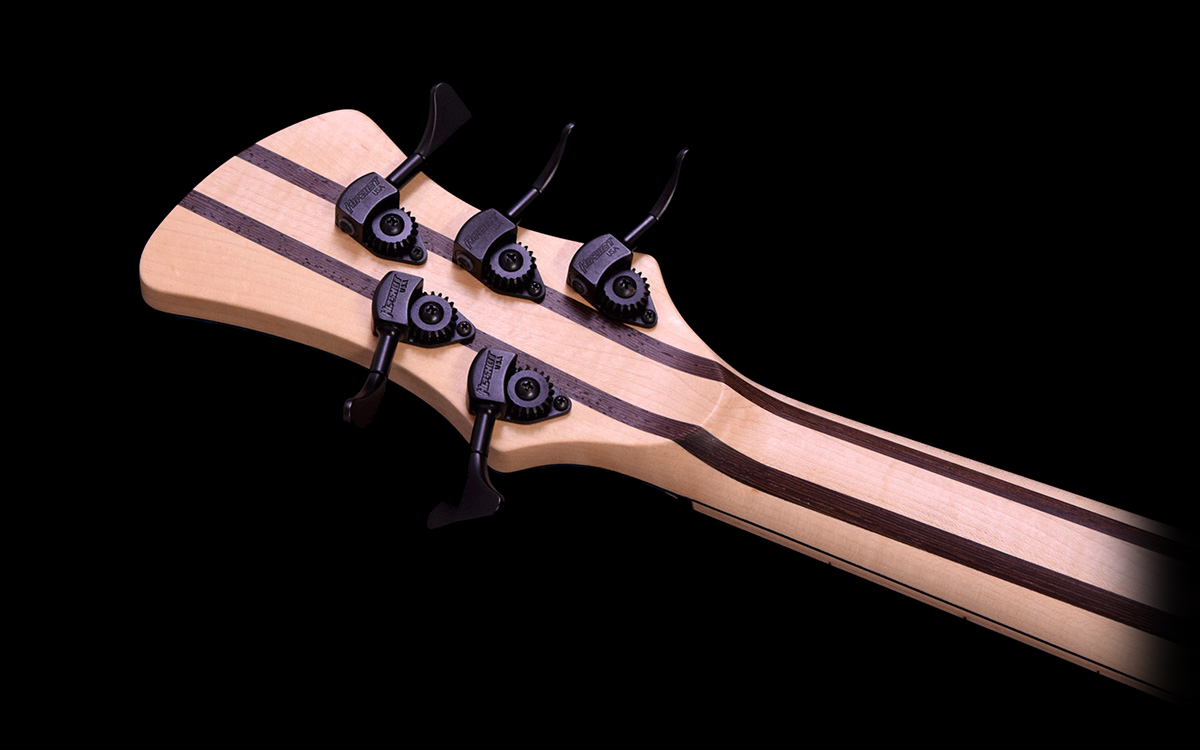
These processes add a key quality aspect to our instruments. Whilst this is not something you will see or feel when playing one of our basses, if you own an Adamovic you will eventually notice how little work and neck adjustments they need, even when used extensively for many years .